PET Recycling Machine
Inquire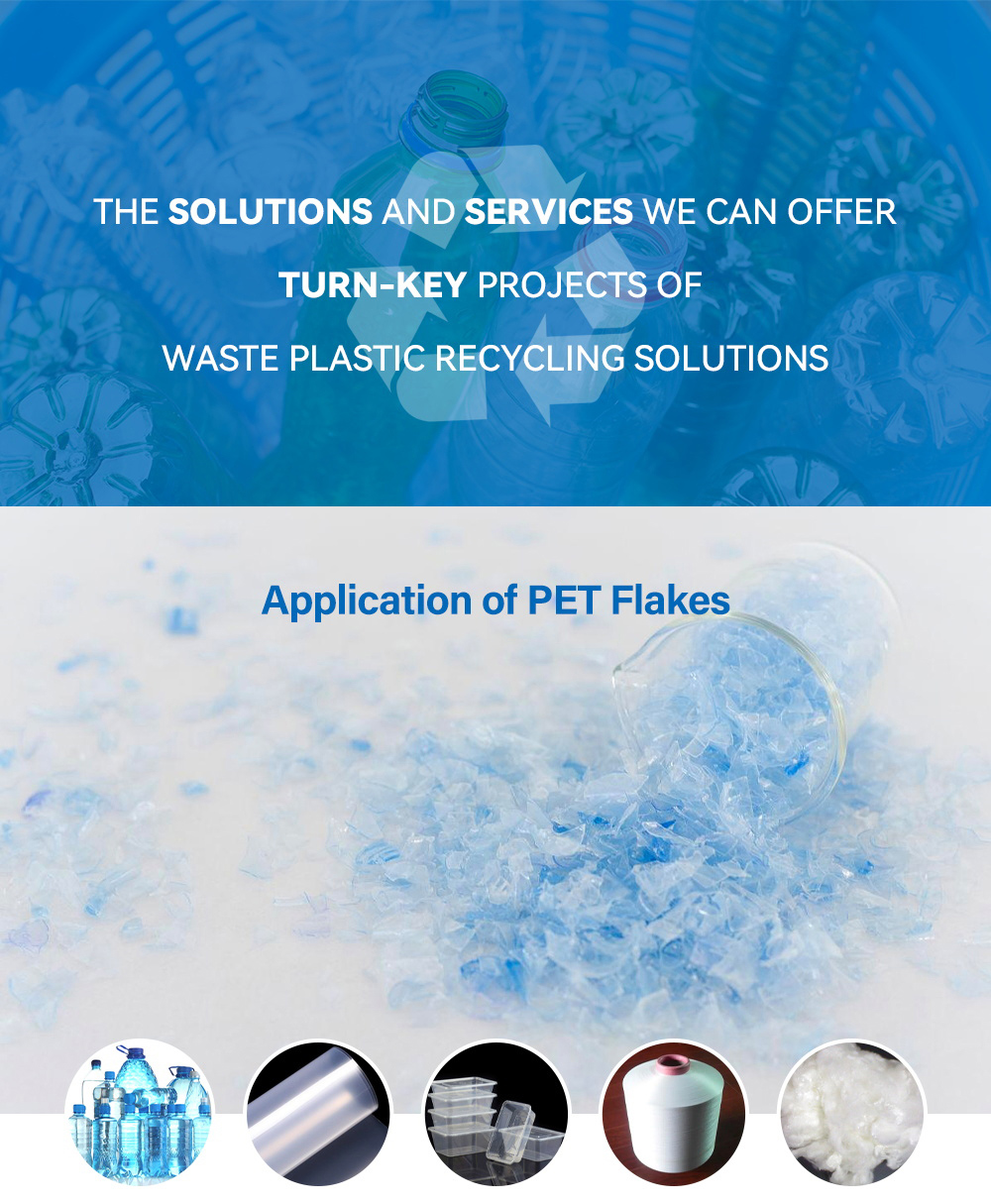
80% to make PSF(polyester fiber)
15% to makepacking blelt
5% to make bottles and others
PET Bottle Recycling Ratio
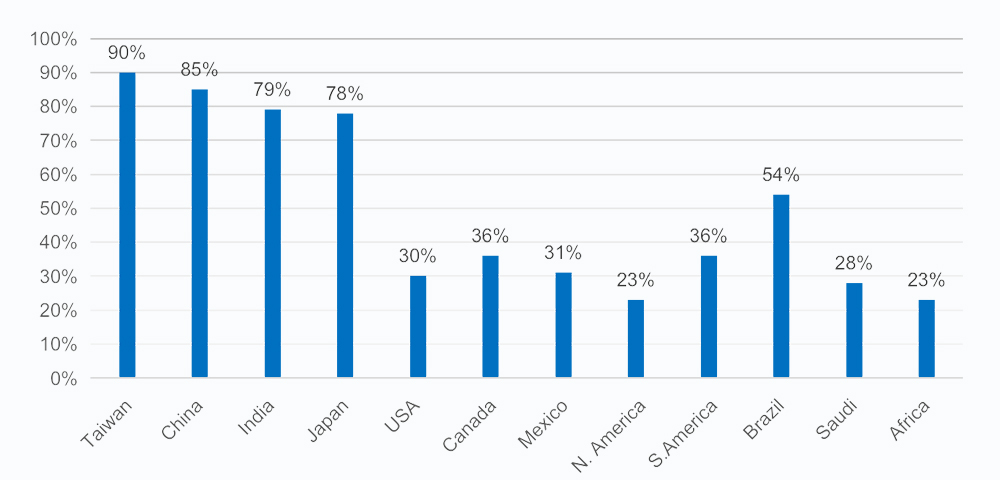
Trends of the Industries
Quality |
Application Aditional |
Value |
High |
Bottle to Bottle |
High |
Film or Sheet |
||
POY |
||
Mono-Filament, High quality PSF |
||
Low Grade Straps |
||
Low grade PSF |
||
Low |
Paint |
Low |
To make bottle to bottle grade material with reasonable investment and conversion.
Contaminants
Caps, Rings | Residual Beverage | Label(PVC, OPS, BOPP, Paper) | Glue
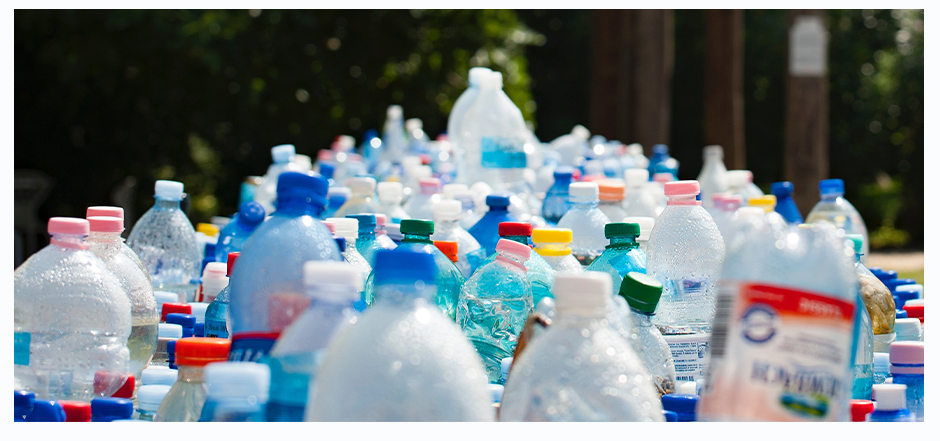
Mud, Sand, Oil, Color bottles, Other Polymer
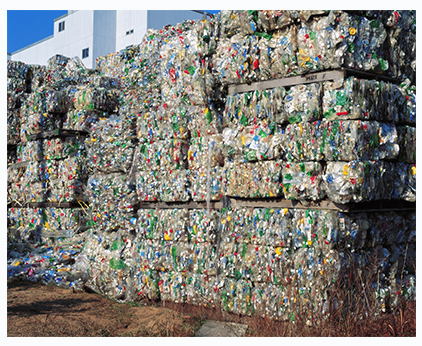
More than 50% PVC L .abel
Some PVC bottles
Pre-sorted With Heavy Mud,
Unforeseen Contaminants in the bottle
30% PVC labels
Presorted with separated color,
Non-regular PET contaminants
Aluminum Caps and Rings
Bottle from Recycled Material
PET Washing Recycling Line
It is currently a non-standard product,it will be highly customized solutions based on customer applications for cross-industry investors, it takes a long time to study. In order to solve this problem, Polytime Machinery has launched a modular cleaning unit for customers to choose from,which helps make effective combinations to quickly form the entire line design based on the characteristics of raw materials.Modular equipment can reduce equipment footprint and save design costs. Polytime Machinery's strong R&D team innovates in technology and discusses progress with customers.
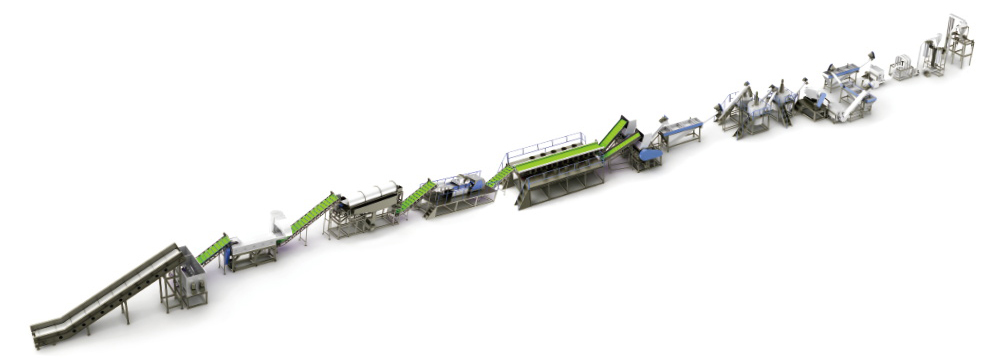
01 Debaler
02 Label Remover
03 Pre- washer
04 Optical Sorter
05 Manual Sorting Platform
06 Crusher
07 Friction Washer
08 Floating Separation Tank
09 Friction Washer
10 Hot Washing System
11 High Speed Friction Washer
12 Centrifugal Dryer
13 Floating Filtering Washing Tank
14 Dewatering Dryer
15 Thermol Pipe Line Dryer
16 Dust&label Separator
17 Weighing Package Hopper
POLYTIME machinery provides customized production line design accordingly. Through the analysis of raw materials and customers' requirements for the final product to optimize the configuration of the production line.Use the latest technology to promote the world's transition to sustainable energy.
- Technical Parameter -
Capacity & Basic Information
Standard plant size (output): 500kg/h, 1000kg/h, 2000kg/h, 3000kg/h, 5000kg/h
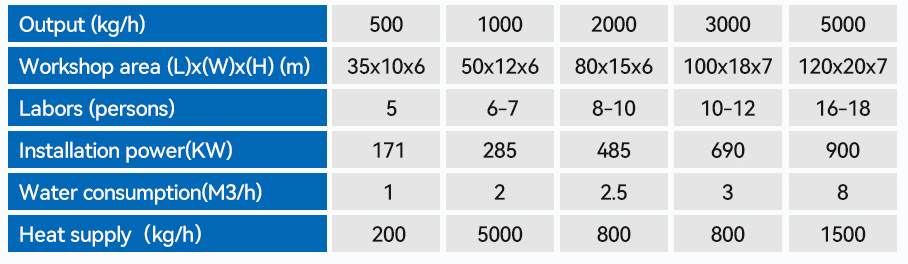
Materials Requirements
Project needs adjustment according to the condition of materials
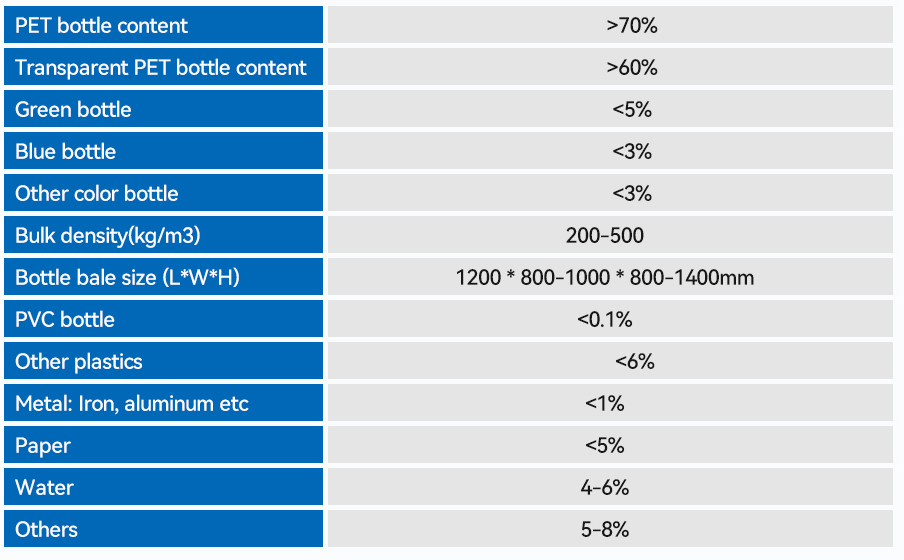
Specs of end products --- PET flakes
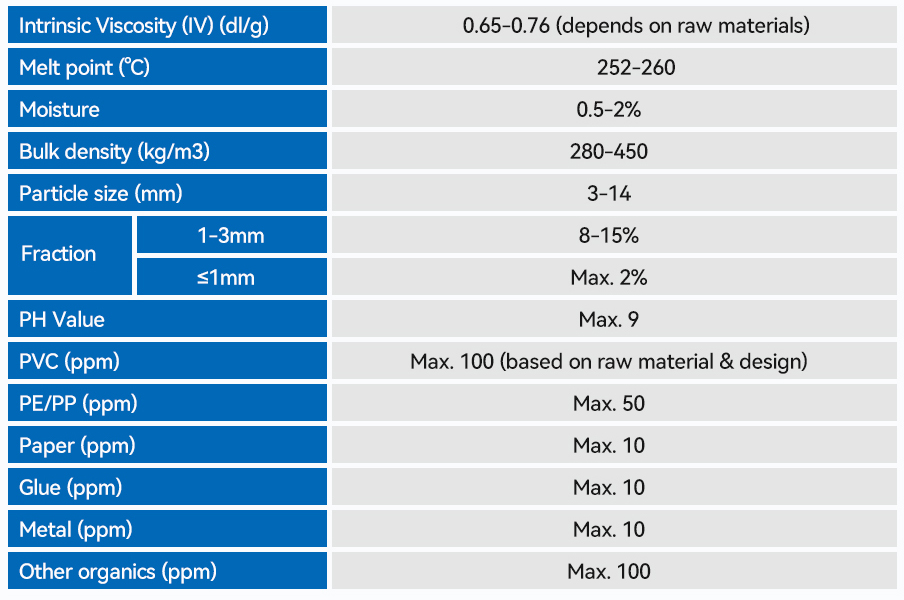
- Advantage -
Inclined Conveyor Feed Belt
Inverter control
The edge is sealed by PVC sealing, which is
not easy to wear and has long use life.
Adopt rubber or PVC, equipped with barrier
strip as option.
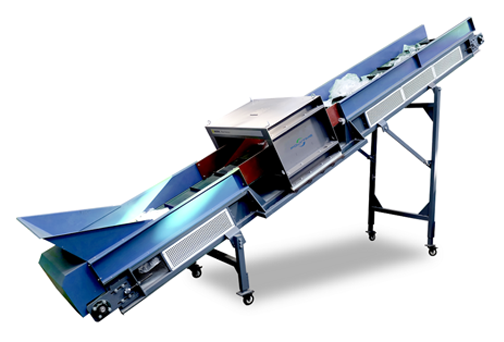
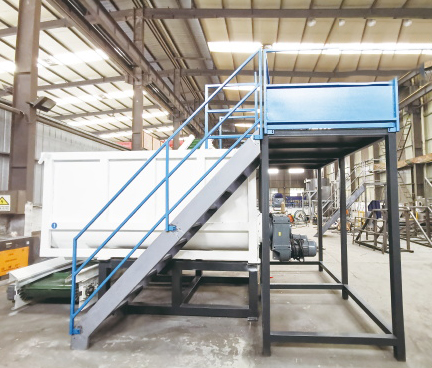
De-baler & Weighing Section
Manually cut off the bundling wire or the straps, using a forklift to put the bale into the chain plate conveyor.The bottle bricks are spread out to a certain extent, storing a certain amount of raw materials a to ensure the uniformity and continuity of washing line feeding.
Trommel & Metal Removing Section
The high-performance trommel is used to separate the sundries, stones, glass, metal stuff and other impurities in the raw materials to reduce the production pressure in the later stage, reducing equipment wear and capacity consumption, and effectively improve product quality.
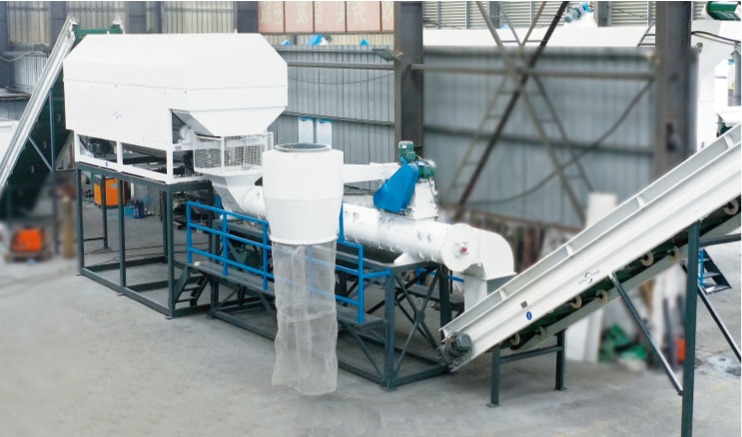
Pre-selection & L abel Separation Unit
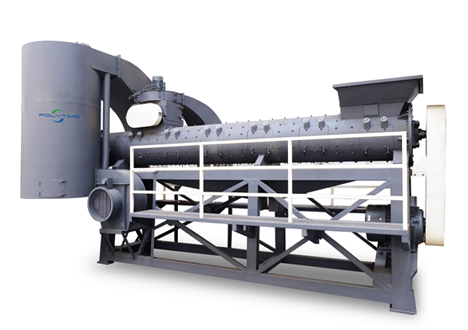
With manual sorting, variegated impurity bottles will be selected to a large extent.Label remover will rub each bottle in turn at high speed, destroying the label attached to the bottle body.The label baling system is used to pack the separated labels and films, effectively reducing the occupation of human space.
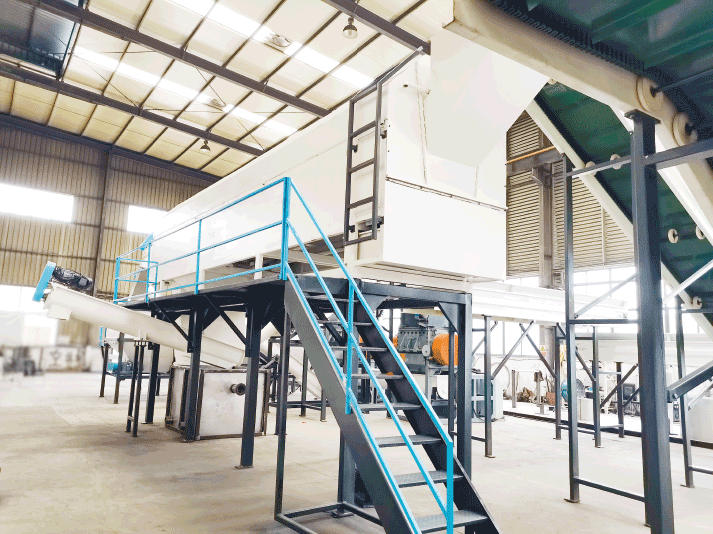
Bottle Pre-washing Section
Under powerful stirring, the continuous bottle washing machine which combined the power functions of machinery, chemistry and heat energy will separate and remove over 90% impurities. Afterwards process equipment will be protected properly due to purified bottle bodies.
Wet-Crusher Section
When we pour water with material to crushing chamber, the friction between crushed flakes and crusher rotor will cause first step of flake washing. And most of contaminants will be separated from flakes. Even for adhesive labels, many of them will also be removed from flake surface. On the other hand, the water pouring will reduce the temperature of crushing chamber. It protects the life time of rotor, blades and bearing.
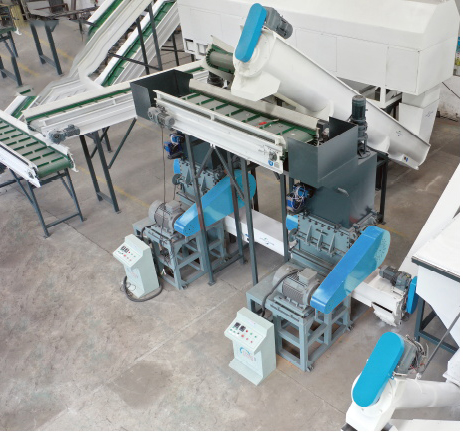
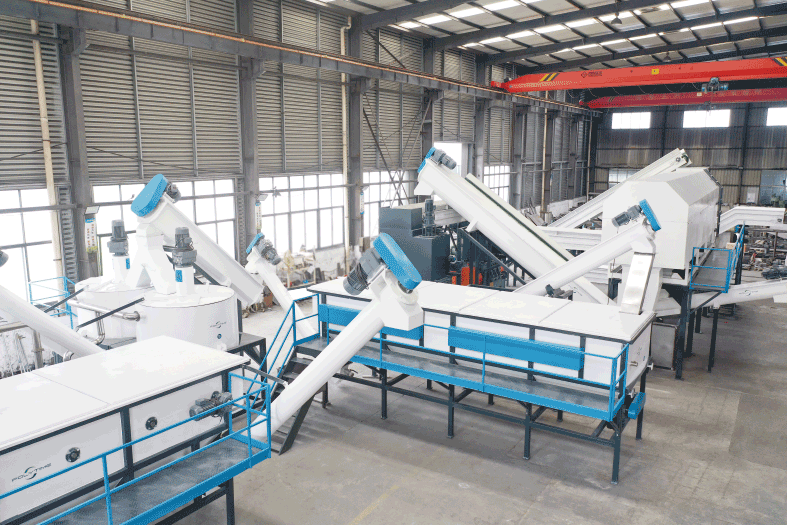
Water Separation Section
The bottle body is crushed together with the cap and the ring, which is mainly PP/PE material.Mixed fragments after grinding use the difference in specific gravity between different plastics,water separation tank will cause the PET flakes to sink and the bottle caps to float, while cleaning the PET flakes for the first stage.PP/PE material will be collected as a by-product.
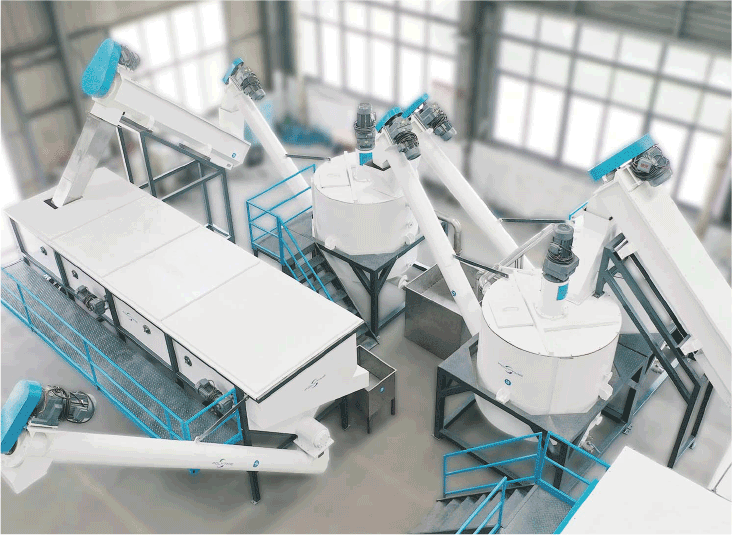
Hot Washer & Friction Washer Section
Thermal, chemical and mechanical forces will be used in hot washer. The friction between the bottle flakes and the shearing force of the vortex of the medicine solution are used to remove impurities from the surface of the flakes and remove it by centrifugal dehydration.With continuous friction washer, floating washer and centrifugal dryer, chemical on the surface of the flakes will be cleaned, and the PH value of the flakes will be neutral near.
Friction washer (low speed and high speed)
Low Speed type
With speed of 600rpm;
With the function of feeding;
Dewatering, surface sludge removal.
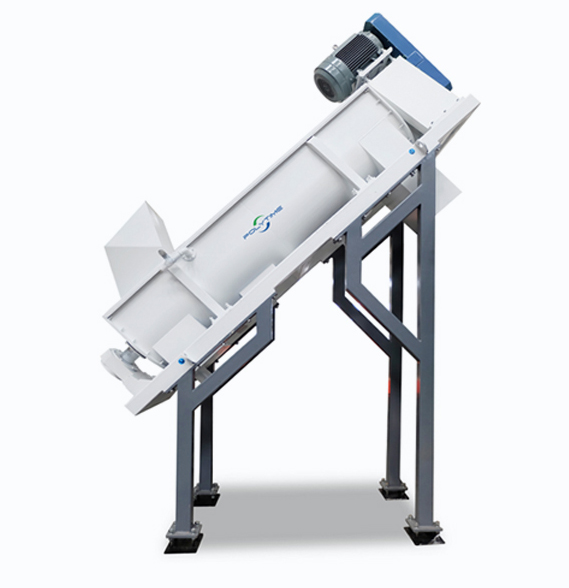
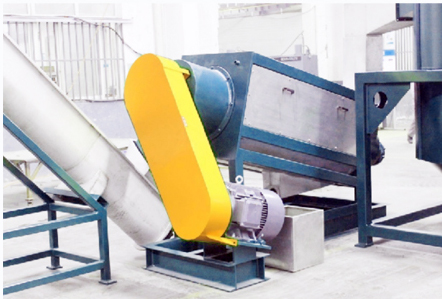
High Speed type
With speed of 1200rpm;
Fast friction;
Dewatering, surface sludge removal.
Centrifugal dryer--- Dewatering
High speed dynamic balance treated with speed up to 2400rpm.
Moisture content less than 1.5%.
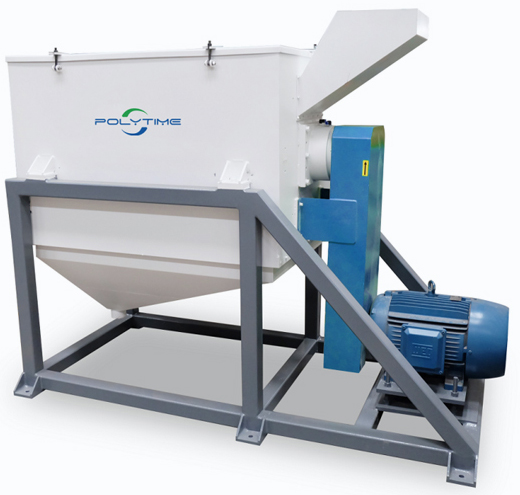
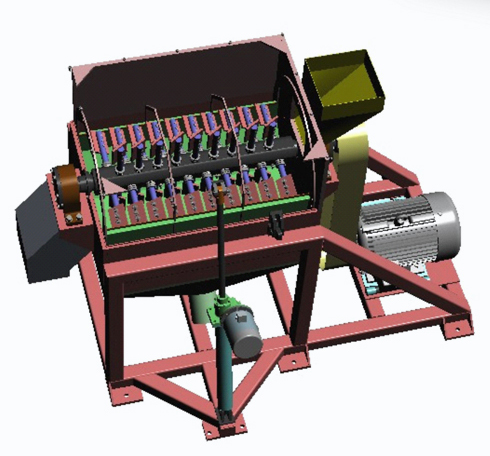
Inner shaft is made by 45# steel and nickel chrome plated ensures abrasion resistance and toughness.
Blade angle is adjustable to meet flakes of different water conte.
Label Separation Section and package system
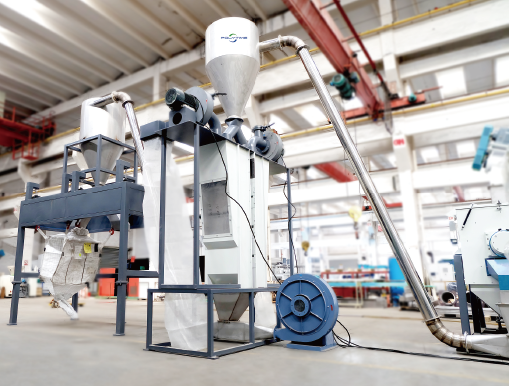
Separate the thin film, powder and other light materials in the bottle flakes by air blow control.Shake solid, measured and weighed.
Metal Processing Unit
Magnetic metal separation:
1. Permanent magnetic belt style de-ironing separator, 0.1-35KG ,iron filings, iron.
2. Permanent magnetic drum-style sorting machine. Magnetic field intensity: 400-600GS
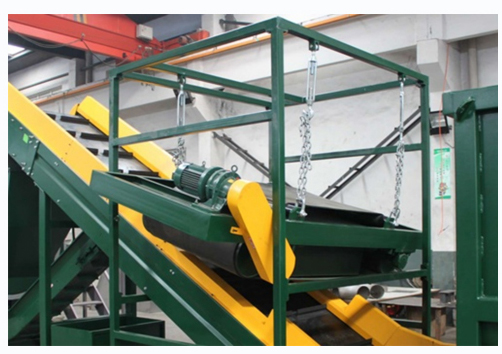
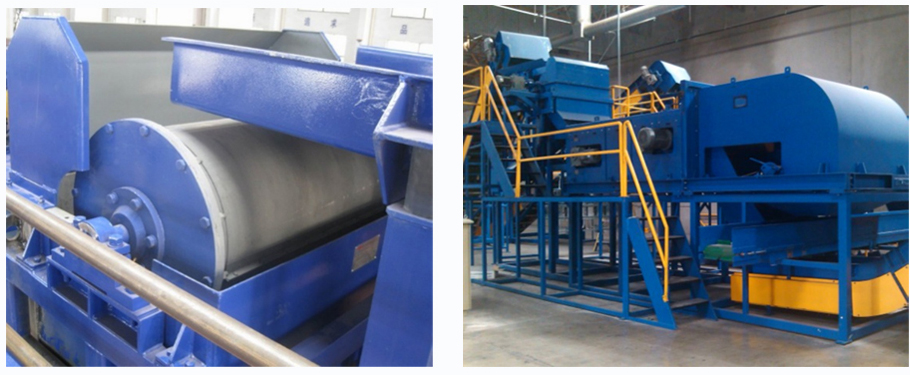
Non-magnetic non-ferrous:
Metal eddy current sorting machine:
1. It can be adapted to wide range of material sizes
2. Good property of demagnetization.
Intelligent Optical Sorting Equipment
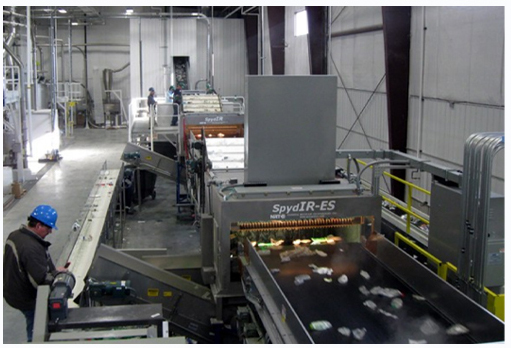
Some Global Main Suppliers:
NRT, USA (NIR);
T-TECH Germany (NIR);
MSS, USA (NIR);
Pellec France (NIR);
S+S, Germany (NIR);
MST, China (X-Ray).TOMRA
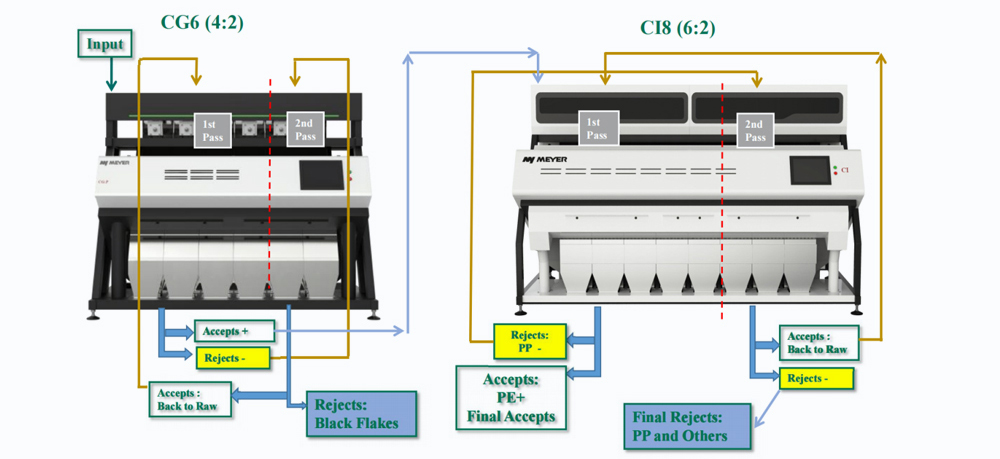